Ever thought about how mold temperature affects optical lens quality in Injection Molding Optical Lenses? In the world of optical engineering, knowing this link is key. We’ll look into the THY Precision Injection Molding Optical Lenses process and see how controlling temperature helps make top-notch optical lenses. These lenses are used in many areas, from consumer products to industrial tools.
Key Takeaways
- Mold temperature is crucial in making optical lenses through Injection Molding Optical Lenses.
- It’s important to keep the mold temperature even for the best lens quality.
- Using simulations and experiments can fine-tune the molding process.
- After molding, compression can be used to make lenses more accurate.
- Knowing the steps of the Injection Molding Optical Lenses process is key to making great optical lenses.
Introduction to Injection Molding Optical Lenses Process
Injection Molding Optical Lenses is a key method for making many plastic parts, from gadgets to car parts. It uses molten plastic that cools and solidifies in a mold to form the desired shape. Knowing the injection moulding process step by step is key for making high-quality parts.
The Injection Molding Optical Lenses Cycle: A Synchronized Dance
The plastic Injection Molding Optical Lenses process has a detailed cycle. This cycle makes sure the final part is made efficiently and precisely. Let’s look at the steps of the molding cycle:
- Mold Design: The mold shapes the final product. Good mold design thinks about the part’s shape, how the plastic flows, and how it cools.
- Resin Selection: Picking the right resin is important. It affects the part’s strength, heat resistance, and look. Cost, availability, and how easy it is to process are also considered.
- Clamping Unit: This unit keeps the mold together during the process, handling the high pressure needed to fill the mold.
- Injection Unit: This unit melts the plastic pellets into a molten state. Then, it pushes this material into the mold under high pressure.
- Cooling Unit: As the plastic cools and hardens in the mold, the cooling unit helps keep the temperature right. This ensures the part stays the right size and shape.
- Part Ejection: After cooling, the part ejection system takes the finished product out of the mold, ready for more steps or assembly.
Understanding the injection moulding process step by step helps manufacturers make better parts. It improves quality and makes production more efficient.
Stage | Description |
---|---|
Mold Design | Considers part geometry, plastic flow, and cooling requirements |
Resin Selection | Determines the mechanical, thermal, and aesthetic properties of the final part |
Clamping Unit | Holds the mold halves together during the injection and cooling stages |
Injection Unit | Melts the plastic pellets and injects the molten material into the mold cavity |
Cooling Unit | Maintains the desired temperature and ensures the part’s dimensional stability |
Part Ejection | Releases the finished product from the mold for further processing or assembly |
By getting good at the injection moulding process step by step, THY Precision can make better plastic parts. This deep knowledge helps the company make high-quality parts, improve its processes, and stay competitive.
Factors Affecting Lens Quality
Creating high-quality optical lenses through injection molding needs careful attention to several factors. One key factor is residual birefringence. This is a measure of how the material’s optical properties vary. It can cause unwanted distortions and flaws in the lenses.
Residual Birefringence in plastic injection molding
Residual birefringence in lenses comes from two main causes: flow-induced and thermal-induced. During molding, the plastic is heated, pushed into the mold, packed to fill the space, and then cooled. These steps can create stresses inside the plastic, leading to residual birefringence.
Knowing what causes residual birefringence in injection moulding process step by step is key to making better lenses. Important things like mold design, the type of plastic used, how the mold is clamped, how plastic is injected, and how it cools affect this issue.
Factor | Impact on Residual Birefringence |
---|---|
Mold Design | Good mold design, including where the gate is and the shape of the cavity, can lessen flow-induced birefringence. |
Resin Selection | Picking a polymer resin with less inherent birefringence can cut down on residual birefringence in the final product. |
Clamping Unit | A well-working clamping unit ensures the mold fills evenly, reducing flow-induced stresses. |
Injection Unit | Right settings for injection, like shot size and speed, can help prevent flow-induced birefringence. |
Cooling Unit | Good cooling unit design and control can manage thermal-induced residual birefringence by controlling cooling rates and mold temperatures. |
By managing these key factors in the injection moulding process step by step, makers can improve the quality of lenses made by injection molding. This helps reduce the effects of residual birefringence.
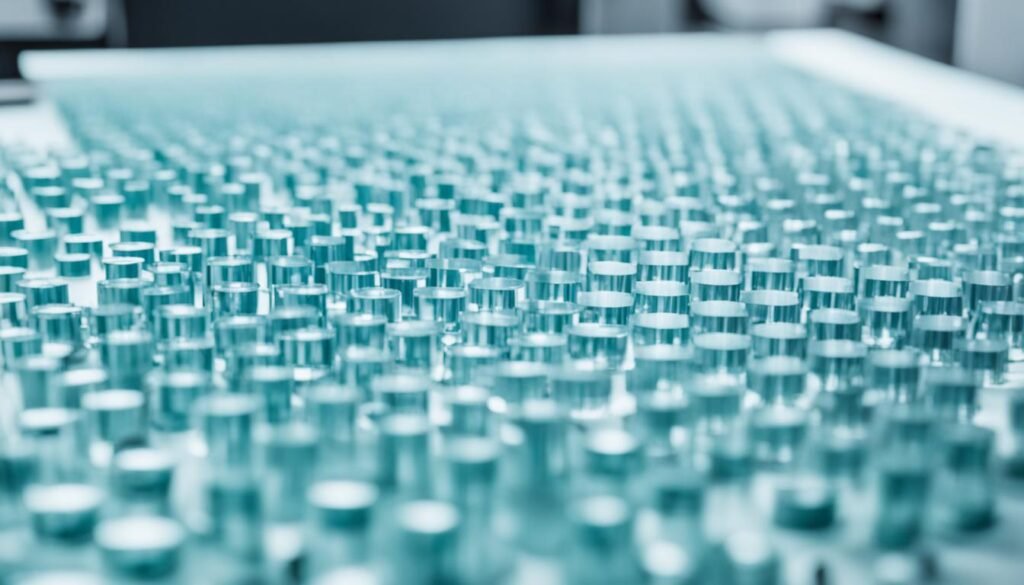
Experimental Setup and Materials
At THY Precision, we’re always looking to improve plastic injection molding technology. We use the cycle olefin polymer (COP) ZEONEX 480R from Zeon Corp., Japan, for our lenses. This material is great because it’s clear, resists heat well, doesn’t absorb much water, has low birefringence, and is very resistant to chemicals.
We designed a special two-cavity mold to see how cooling affects our plastic parts. The mold has different cooling channels around each cavity. It has a plano-convex shape, is 25 mm wide, has a 70 mm curve, and is 1.125 mm thick.
Mold Design and Materials for injection moulding process step by step
The design of the mold is key to making high-quality plastic parts. At THY Precision, we picked the right materials and design for our molds. This lets us study how different cooling channels affect our lenses.
We chose materials that work well with the ZEONEX 480R resin. This ensures our molds perform consistently during the molding process. By doing this, we get lenses with great optical quality, precise dimensions, and high quality.
Our careful choice in mold design and materials means we can make top-notch optical lenses. At THY Precision, we focus on innovation and quality control. This ensures every step of the molding process is done right for the best results.
Mold Temperature Distribution and Part Displacement
At THY Precision, we focus on making our plastic injection molding process perfect. We make sure the mold temperature is even and the part fits just right. We use advanced 3D simulations to watch how the mold temperature and part shape work together during the molding cycle.
We use a special flow-through layout type of cooling channels for even temperature in each cavity. This lets us adjust things like the runner distance and cooling channel size for perfect temperature control. This careful mold design is key for making high-quality optical lenses.
Dealing with geometric surface issues is a big challenge in making top-notch injection-molded lenses. At THY Precision, we’ve put a lot of effort into solving these problems. Our team is always finding new ways to improve our process for our clients.
Process Parameter | Impact on Mold Temperature Distribution | Impact on Part Displacement |
---|---|---|
Mold Design | Optimal cooling channel layout ensures uniform temperature distribution across the cavity. | Precise mold design minimizes geometric deviations and warpage in the final part. |
Resin Selection | The thermal properties of the chosen resin influence the mold temperature profile. | Resin characteristics, such as shrinkage and flow behavior, impact part displacement and warpage. |
Injection Unit | The injection unit controls the melt temperature and flow rate, affecting the mold temperature distribution. | Injection parameters like speed and pressure influence the part deformation and displacement. |
At THY Precision, we’re all about delivering top-notch optical lens quality. We focus on the injection moulding process step by step. By keeping mold temperatures even and reducing part displacement, we make sure our products are precise and meet the highest standards.
injection moulding process step by step and Optical Lens Quality
The injection moulding process is key for making high-quality optical lenses. It has many steps that must be done right for top-notch products. At THY Precision, we know how the plastic injection molding process affects optical lens quality.
The molding cycle starts with picking the right resin for the lens. Then, the mold design is made to shape and cool the lens just right. The clamping unit, injection unit, and cooling unit work together to make a consistent, high-quality product.
Keeping the mold temperature right is key for optical lens quality. The right temperature helps reduce birefringence, which can affect the lens’s clarity. Our team at THY Precision keeps a close eye on the mold temperature to meet our clients’ high standards.
The part ejection and quality control stages are also vital. We use advanced methods and tech to check each lens closely. This ensures we only send top-quality lenses to our customers.
At THY Precision, we aim to give our clients the best optical lens quality. We use the latest tech, strict quality checks, and deep plastic injection molding knowledge. This way, we always meet and beat our customers’ expectations.
Compression Molding for Post-Processing
The injection moulding process step by step is often used to make optical lenses. But, it can leave behind stresses and birefringence that affect the quality. Compression molding is a new way to fix this.
For over thirty years, compression molding has been improving. It makes parts with much less stress than plastic injection molding. This is great for reducing the stresses and birefringence in optical lenses.
Birefringence Relaxation through Compression Molding
Studies now show that compression molding works well for reducing stress and birefringence in small glass lenses. The high mold temperature and slow cooling in compression molding help relax the stresses. This leads to better optical quality in lenses.
Using compression molding, makers can improve the quality control of injection-molded lenses. This ensures they work well in high-tech uses like advanced cameras and augmented reality.
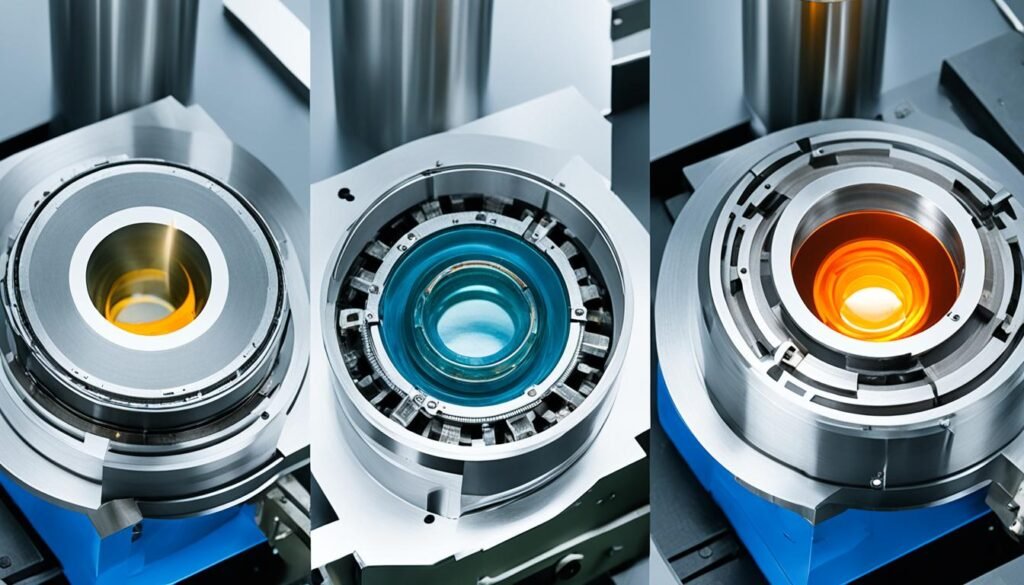
“Compression molding has been widely adopted for the manufacture of small aspheric glass lenses, where low residual stresses and high form accuracy can be achieved.”
Adding compression molding after injection molding is a big step forward. It helps with mold design and resin selection in the clamping unit, injection unit, and cooling unit of plastic injection molding. This method ensures better part ejection and high-quality optical parts.
Conclusion
The injection moulding process step by step is key to making high-quality optical lenses. It’s important to fine-tune plastic injection molding aspects like mold design, resin selection, and molding cycle control. This ensures even mold temperatures and reduces birefringence in the lenses.
Designing the clamping unit, injection unit, and cooling unit right is vital. It helps with consistent part ejection and keeps quality control tight in the injection moulding process step by step. With these steps, THY Precision can make top-notch optical lenses that meet industry standards.
Also, compression molding after the process can ease birefringence in the lenses. This makes birefringence-free plastic lenses with great accuracy. By optimizing the injection moulding process step by step and adding post-compression-molding, THY Precision can always deliver lenses that go beyond what customers expect.